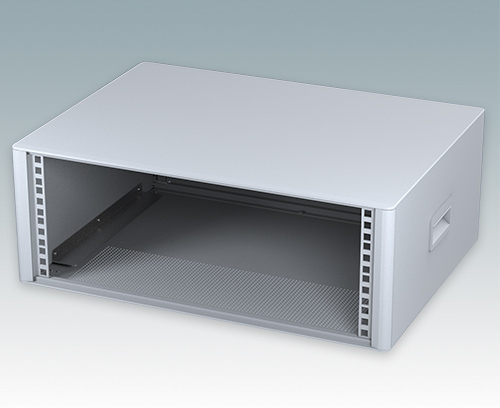
-
Enclosures
Enclosures Electronic enclosures | 19 inch rack mount enclosures
Versatile range including desktop enclosures; small instrument cases; portable enclosures with tilt and swivel carry handle bar; 19" rack mount enclosures and wall mount enclosures.
Metal Enclosures Modern metal enclosures for OEM electronics equipmentFor desktop, wall mount, portable and 19" rack mounted electronics equipment. All manufactured from high quality aluminium.
-
Accessories
Accessories Accessories for METCASE electronic enclosures and others
View the extensive range of accessories: 19" front panels, handles, enclosure feet kits, PCB guides and fixings.
Accessories for Enclosures Extensive range of universal accessories19" front panels, enclosure feet kits, PCB guides and 19" mounting kits.
Accessories for 19" Racks Universal accessories for 19" equipmentRange of universal 19" rack shelves, 19" front panels and fixings.
-
Custom Enclosures
Custom Enclosures Customised enclosures for OEM Electronics
We can supply fully finished custom electronic enclosures with all the necessary modifications for mounting your PCBs, displays, connectors and other components.
Modifications & Finishing All the customising services you needOur manufacturing site is equipped with all the equipment required to produce fully finished enclosures and front panels - ready for mounting your electronic components.
Bespoke Enclosures Bespoke metal enclosures and sheet metal partsFully bespoke electronic enclosures can be created using our standard case components such as diecastings and extrusion profiles or from fully fabricated sheet metal components.
-
News
News
Full details about all our new products and services along with company news.
NewsPress ReleasesRead our latest company press information and our complete press releases archive.
BlogOur blogs cover industry trends, how to's, customer applications, FAQs, international product standards and details about our new products and services.
-
Technical Info
Technical InformationHere can you download our datasheets, certificates, REACH, RoHS & WEEE statements, assembly instructions and catalogues.
Specifying Customised EnclosuresSpecifying Customised Enclosures
REACH StatementWe are committed to meeting our legal obligations under REACH. Read our statement here.
ROHS / WEEE DirectivesStatement regarding our product compliance with RoHS and WEEE directives.
Discontinued ProductsIf you cannot find a product on our website, check here to see if it has been discontinued.
Temporary-UpdatesTemporary-Updates
-
About Us
About METCASEMETCASE is the metal enclosures division of OKW Enclosures Ltd. Our company is based in Fareham in Hampshire.
Privacy Policy - GDPR (EU) 2016/679OKW's Privacy Policy provides you with information on how we collect and process your personal data when you interact with us via our websites, through emails etc.
Cookie PolicyLearn more about how we use cookies in order to provide you with the best online service and website functionality.
-
Ordering
Ordering InformationFull information on placing an order, getting a quotation or sample, delivery charges, payment terms and typical delivery times.
-
Contact
Contact METCASEFull contact details including opening hours and meet our team. Plus how to make an enquiry or request a quotation and/or a sample.
General Enquiries FormUse our contact form for general enquiries and requests for information, and to upload your documents and pictures.
How To Find UsTravel information if you are visiting our sales and production facilities in Fareham, Hampshire, United Kingdom.
Worldwide Sales NetworkHere you can find your local OKW contact. We have subsidiaries in 8 countries and long-standing sales partners worldwide who are ready to help you.